硬質ウレタンの特長と成型工程features
硬質ウレタンの特長
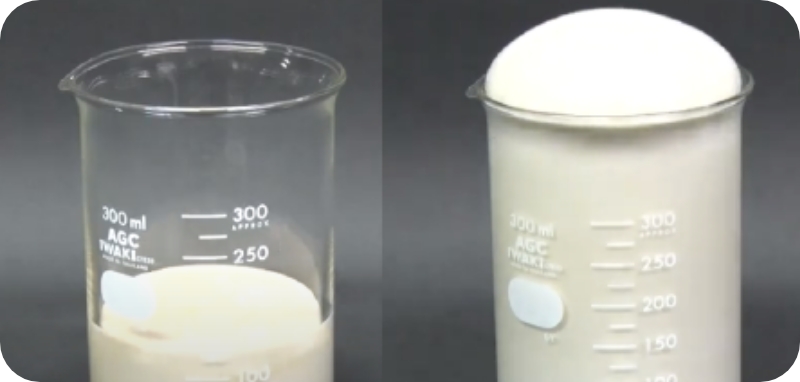
硬質ウレタンの特性
硬質ウレタンは、ポリオールとイソシアネートという2つの原料を混ぜ合わせた際の化学反応によって成型されます。発泡成型の場合は、硬化時の泡化作用で発生した微細な無数の気泡を内部に閉じ込めることにより、高い断熱性能、耐久性、軽量性などの多くの特性が生まれます。
一般的にはウレタンは軟らかいスポンジと理解される傾向ですが、ヘルメスで扱っているウレタンは、特性的に汎用プラスチックに近い硬質ウレタンになります。硬質ウレタンの長所・短所は多々ありますが、汎用プラスチックの成形品では難しい偏肉や肉厚の成型品や、金型(モールド)成型で求められる複雑な設計を比較的容易に行うことができます。
設計の自由度も高く少量から生産が可能な硬質ウレタン成型品の可能性はお客さまの独創的なアイデアを待っています。
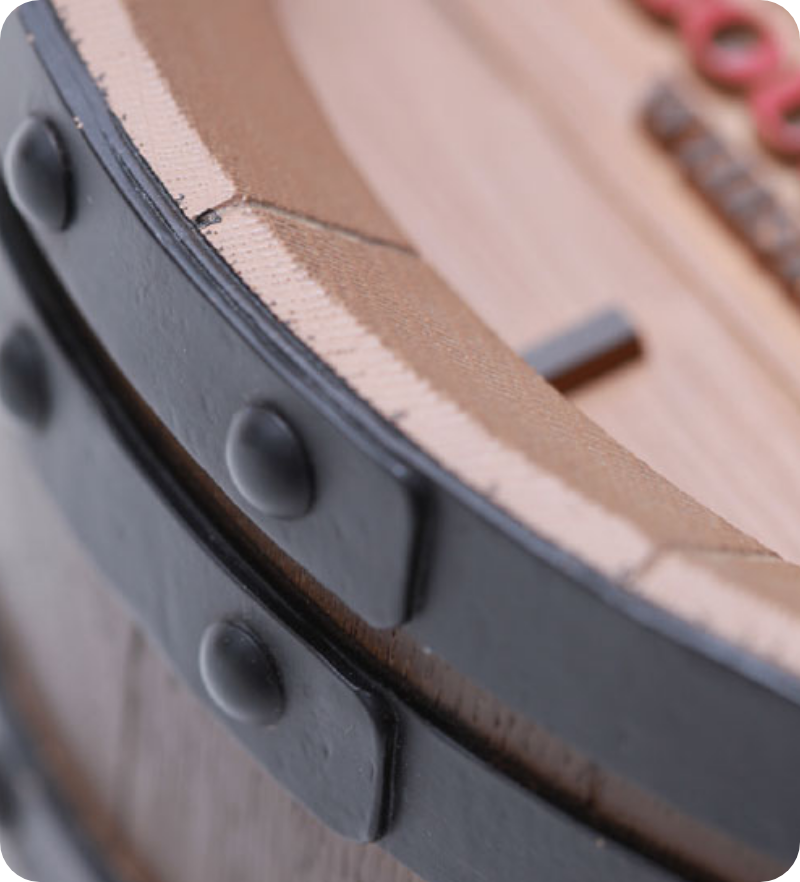
硬質ウレタンのメリット
硬質ウレタン成型品は高い汎用性を誇ります。その用途は、汎用プラスチックによる成型品よりも設計の自由度が高い工業製品部材、多様な質感と形状をリアルに再現した店頭広告商品・装飾品やエクステリア用品、極少量の生産しか必要のない医療機器や医療用検査機器などの外装カバーなど、見ただけではわかりませんがあらゆる分野に広がっています。
シリコーンゴム型による成型のため、金型(モールド)による成型ほどの寸法公差は対応できませんが、金型成型よりも短期間かつ安価で堅牢性、断熱性、そして素材によっては軽量性などの多くのメリットを提供するのが硬質ウレタン成形品です。もちろん、塗装を施すことによって本物以上にリアルな質感を実現することもできますし、屋外使用に対する耐候性も向上します。
硬質ウレタンの可能性は、お客さまの独創的なアイデアとともにどこまでも広がります。本物の素材では実現できないものでも、アイデア次第でどのようにも具現化することができる — それが硬質ウレタンの最大の魅力です。
材料について
硬質ウレタンの材料は大きく「発泡成型」と「無発泡成型」の2種類に大別できます。
発泡成型 | 比重 約0.2~0.3程度 |
---|---|
無発泡成型 | 比重約1.1程度 |
(※比重が1よりも大きい物は水に沈み、1よりも小さい物は水に浮く)
肉厚について
硬質ウレタン成型の成型品は、他の汎用プラスチック材に比べて耐衝撃強度が高くないため、健全な成型品を製作するためには以下の肉厚が必要です。
平均肉厚 | 部分的な最小肉厚 | |
---|---|---|
発泡成型 | 10mm 以上 | 4mm |
無発泡成型 | 5mm以上 | 2mm |
寸法公差について
シリコーンゴム型による成型では、以下のような寸法公差が必要とされます。
~50mm | 土1.0mm |
---|---|
51~200mm | 土1.5mm |
201~600mm | 土2.5mm |
601~1,000mm | 土3.0mm 以上 |
(※ウレタン樹脂成型品の一般的な線膨張係数はおおよそ8×10です)
メリット・デメリットについて
ウレタン成型には以下のような特性があります。
メリット | デメリット | |
---|---|---|
数量 | 少量生産にも対応。(1ロット20個程度から) | 数量が大量になる場合は、トータルコストで他の成型方法が安価になる可能性があります。 大量生産によるスケールメリットは少ない。 |
モデル | モデル型は木型等で製作しているため比較的短納期でできます。設計の変更など形状変更の場合には、部分的なモデル型修正により短期間で修正可能です。 | 型の耐久性は金型ほど長期間ではありません。 |
形状 | 複雑な形状ほど、経済的効果があります。肉厚品/偏肉品などの成型品の製作が可能。 シリコーンゴム型で成型のため、若干の逆テーバー品でも成型可能。 |
型の耐久性は金型ほど長期間ではありません。 |
設計デザイン | 製品機能・デザインを重視した設計や、加工省略などの設計が自由にできます。 | 射出成型など、他の成型方法の設計図面をそのまま使用することはできません。 |
表面処理 | 塗装による表面処理が可能。 そのため、同じ成型品でバリエーションを増やすことが容易です。 |
原料着色による成型品はできません。 鏡面仕上げは欠点が目立つため、不可能です。 |